CSUB’s delivery garners attention:
The groundbreaking project, Paradis Bridge, is attracting international attention
The world’s longest composite truss bridge was officially opened in Bergen, Norway in November. It paves the way for composite material as an innovative and viable alternative in infrastructure. The bridge in Bergen is the result of a successful collaboration between CSUB, Consto, and FiReCo, along with the customer, Vestland County Municipality.
– This is a milestone for CSUB, as it represents a very special use of composite materials. This bridge is unique due to its size, as this material is not typically used for such large bridges. The process of creating a composite truss bridge is entirely special. It is complex, but we have managed to execute it safely and securely, says CSUB’s Technical Director, Jon Inge Brattekås.
The engineering department started designing the composite bridge two years ago. Over the last nine months the manufacturing of the bridge has been CSUB’s main focus.
– Paradis Bridge consists of around 1,200 components in total, most of them not visible when looking at the bridge today. Few other companies in Norway could have undertaken this work; one would have to look further into Europe to find such expertise, says Frode Langnes, Head of Production.
– This bridge involves large and thick castings. Everything is custom-made using fiber and is then vacuum-injected, resulting in a much stronger and more homogeneous laminate. The use of vacuum injection is also very beneficial for workers as it reduces exposure to gases and chemicals compared to other methods, he explains.
Paving way for a new composite future
Composite materials have been used in infrastructure for several years. CSUB’s first composite pedestrian bridge dates back to 2003. However, there is still a lack of standards for the material, and significant work is being made both nationally and internationally to ensure that standards will be made. The collaborative project on the Paradis truss bridge contributes in this work.
– Paradis Bridge has been very exciting and interesting. While at the same time being challenging in many ways, because no one has done this before. It is pioneering work, and the collaboration to achieve this result has been very rewarding, says Alf Egil Jensen, CEO of FiReCo, about the project.
FiReCo has been responsible for the detailed design of the bridge. The company has over 30 years of experience with composite materials. Being a driving force to establish standards and guidelines for composite, and being able to continue this work through projects such as Paradis Bridge, motivates the company.
– This is how we’ve always operated, seeking projects such as Paradis Bridge. We’re seeing that composite is being used more and more. In construction and civil engineering there is a growing interest, most likely due to the increased focus on reducing CO2. We’re positive and optimistic about the future of the material, says Jensen.
– We’ve worked closely with FiReCo, Vestland County Municipality, and Consto throughout the drafting, production drawings, and approval drawings for the Norwegian Public Roads Administration. For this project, the drawings had to be very specifically detailed to ensure correct fiber placement. Additionally, we conducted numerous tests along the way, so it has been a significant big project, says Kjetil Grøsle, CSUB’s Senior engineer.
Present at the grand opening in November was also the Dutch engineer Liesbeth Tromp. With a background from aviation engineering, and now latest civil engineering, Tromp is at the forefront of establishing international standards for composites. She praises the work behind Paradis Bridge.
– This project is fantastic! Finally, we have a breakthrough towards larger, more complex composite structures. This is now the largest bridge of its kind, and it increases the span and capacity for bridges built with this material, she commends.
Installed in under an hour
Paradis Bridge was built and assembled entirely at CSUB in Arendal before being transported over 450 kilometers to the city of Bergen. The actual installation, which was over a very busy road and train track, took less than an hour. Minimizing traffic disruptions in the area.
– Using a different material would have required on-site construction activity for three to four months. We transported the bridge in one piece and installed it in an hour. That’s very impressive for such a large structure, says Brattekås.
But lightweight and prefabrication are only two of the material’s advantages.
– The bridge is virtually maintenance-free. You don’t encounter the backlog of maintenance costs that often accompanies other materials. Costs that are frequently overlooked but become apparent when bridges reach the age of 30-50 years, explains Jensen and adds: – Those expenses will never come if you choose a composite structure.
Tromp highlights the environmental and lifecycle benefits of the material.
– This material has a very long lifespan, which is extremely valuable in regards sustainability. A bridge like this will last 100 years. If the infrastructure changes, the bridge can be reused elsewhere. After its lifespan the material can be recycled to create new composite structures. I believe this project also demonstrates that we can increase the span and capacity of the bridges we build. This is a pedestrian bridge, but we can go larger, and the material can be used for traffic bridges.
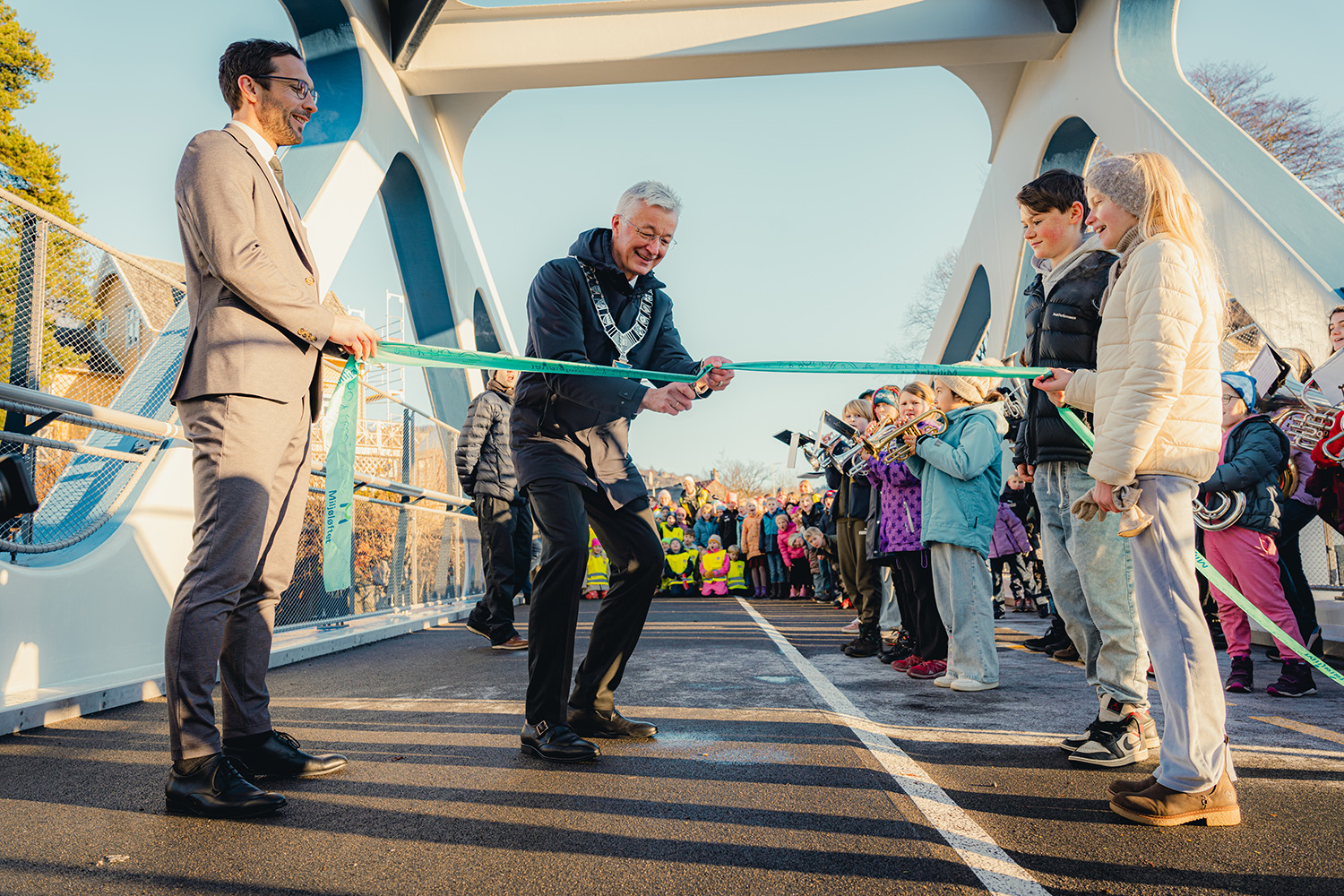
A very satisfied client
The grand opening was accompanied by marching band music and cheers. Over 500 people attended the significant event. And it was a very pleased client that finally could see the bridge being put into use.
– This was one of the reasons I joined the County Municipality four years ago, and now it’s finally here, says Håkon Tryti Nilssen, the project manager from the County Municipality.
He says the County Municipality is very satisfied with the collaboration and the positive experiences gained so far. He states that they have saved an estimated 50% CO2 by choosing a composite bridge over a traditional concrete bridge.
– Although that wasn’t the main drive behind this particular project, we’ve gathered experiences and learnings which we’ll save for later and has noted composite as a good alternative. This is a new tool in the toolbox that we can consider alongside steel, concrete, and aluminum.
The project’s growing into something so large and comprehensive, in the means of paving the way for composite, was not something they had expected.
– Initially, we hadn’t anticipated it becoming as impactful as it did. But we see that projects like this are important. Not necessarily to challenge today’s regulations, but it’s crucial that the regulations evolve as technology advances and new opportunities arise. But we’re taking no risks; this bridge has been thoroughly tested, we’ve even had a 6.5-ton truck out, he assures.
– This is a fantastic project, and the international recognition the bridge has received support that. In Norway, there has been less attention, not many understand how big this project actually is. The bridge is the largest of its kind in the world, Nilssen continues.
The general contractor, Consto, is also impressed by composite.
– This project initially seemed like it wouldn’t be a great fit for us. But then we connected with FiReCo and CSUB, and they introduced some great ideas that made it exciting to participate in. The project has been incredibly educational. Typically, Consto build bridges with concrete or steel, so this material is entirely new to us. We’ve now seen that it has many advantages, says Consto’s CEO, Øystein Mehl Eide, elaborating: – This project has an X-factor. Something that initially seems like an impossible task becomes achievable if you break it up into smaller tasks. This project demonstrates that.
– Forward-looking projects such as Paradis Bridge is part of the CSUB’s spirit. We have paved the way for composite solutions in the subsea industry and aquaculture sector, and now we’re paving the way in infrastructure. We feel like pioneers when it comes to introducing composite material in unconventional areas and have achieved significant breakthroughs in recent years, Brattekås concludes.